Dans un contexte où la rapidité de livraison et la maîtrise des coûts sont devenues des arguments de compétitivité majeurs, l’optimisation flux entrepôt se révèle être un formidable levier de performance pour toute entreprise disposant d’une activité de stockage, de préparation ou de distribution. Au-delà de la simple réduction des mètres carrés occupés, il s’agit d’orchestrer les flux physiques, informationnels et financiers de façon harmonieuse pour servir la supply chain globale, satisfaire le client et préserver la trésorerie.
Les lignes qui suivent approfondissent les dix leviers incontournables de l’optimisation, enrichis d’exemples concrets, de bonnes pratiques terrain et de retours d’expérience issus de secteurs variés (retail, agroalimentaire, industrie, e-commerce). Objectif : vous fournir un guide pragmatique, exploitable dès demain quel que soit le niveau de maturité de votre organisation.
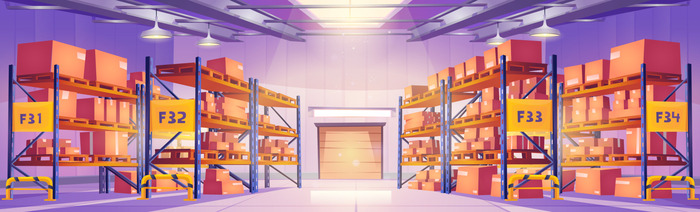
1. Cartographier les flux pour cibler les gisements de productivité
Avant d’investir dans un logiciel ou dans un système de convoyage, il convient de comprendre précisément les chemins que prennent les marchandises, les documents et les opérateurs. Un VSM (Value Stream Mapping) ou une cartographie spaghetti mettent en lumière :
- Les déplacements sans valeur ajoutée (retours en arrière, transports à vide, files d’attente).
- Les points de friction (goulots d’étranglement, ruptures de charge, doublons administratifs).
- Les stocks intermédiaires ou de sécurité surdimensionnés.
Pour maximiser l’impact de cette photographie initiale :
- Collectez des données in situ (observations, chronométrages, interviews d’opérateurs). L’œil terrain détecte souvent des irritants invisibles dans le SI.
- Complétez par des données “machines” : temps d’ouverture de quai, logs WMS, historiques TMS. Une vision 360° fiabilise l’analyse.
- Hiérarchisez les irritants en croisant fréquence, impact financier et impact client. Vous priorisez ainsi les quick wins.
Cas d’usage : un distributeur de pièces détachées a réduit de 37 % la distance parcourue chaque jour par ses préparateurs (-8 km/opérateur) en réorganisant simplement l’implantation de ses bacs A, B et C. Investissement nul, ROI < 2 semaines.
2. Dimensionner la capacité de stockage selon votre mix produits
Le dimensionnement idéal d’une zone de stockage dépend de la courbe ABC : les 20 % de références qui représentent 80 % des volumes doivent être accessibles en quelques pas depuis la zone d’expédition, alors que les produits à faible rotation peuvent être placés en hauteur ou en fond d’allée.
- Analyser la vélocité de chaque article (commandes/mois, saisonnalité, prévisions de ventes).
- Sélectionner un mode de stockage adapté (palettier, drive-in, dynamique, mezzanine).
- Calculer le taux d’occupation cible : entre 80 % et 90 % pour maintenir de la flexibilité.
Pensez également à :
- Reconfigurer les emplacements à l’arrivée de nouvelles gammes (SKU boom). 15 min de re-slotting préventif évitent parfois des heures de recherche en haute saison.
- Intégrer les contraintes règlementaires (zones ATEX, températures dirigées, séparation des produits chimiques). Un incident de conformité coûte plus qu’une optimisation manquée.
Bonnes pratiques : l’usage de bacs standardisés (60×40 cm, 40×30 cm) multiplie par trois la densité d’une zone “pick tower” et simplifie le calcul d’unités de manutention (UoM).
3. Repenser les processus de réception pour réduire le lead-time
Une optimisation flux entrepôt performante démarre dès la porte de quai. La réception est le premier maillon d’une chaîne qui ne peut tolérer les retards ou erreurs.
- Créneau horaire de livraison partagé avec les fournisseurs pour lisser les arrivages, réduire les files de camions et limiter les frais d’attente.
- ASN (Advanced Shipping Notice) : l’avis de pré-expédition envoyé électroniquement permet au WMS de pré-créer les réceptions et d’allouer les ressources humaines.
- Contrôle qualité en ligne (scan code-barres, pesée, prise de dimensions) afin de limiter les retours en stock.
- Cross-docking direct pour les références urgentes ou déjà vendues : produit reçu → colisage immédiat → expédition sans stockage.
Focus sécurité : investissez dans des quais niveleurs récents et un SAS à feux tricolores. Les micro-accidents de quai représentent 25 % des arrêts de travail en logistique.
4. Mettre en place un WMS pour fiabiliser les données et l’allocation des emplacements
Le Warehouse Management System constitue la tour de contrôle de l’entrepôt : il oriente l’humain, pilote les machines, assure la traçabilité et crée la donnée maîtresse utilisée par la finance ou le commerce.
- Système d’adressage chaotique ou fixe selon la volumétrie et la criticité des flux.
- Instruction en temps réel via terminaux RF, PDA, voice picking ou smart-watches.
- Traçabilité unitaire, lot, numéro de série ou palette pour sécuriser la chaîne logistique.
- Intégration plug & play avec TMS, ERP, portails fournisseurs, marketplaces.
Le WMS doit toutefois rester un enableur et non un frein :
- Cartographiez les processus avant paramétrage. Un mauvais process digitalisé devient un mauvais process accéléré.
- Privilégiez une architecture ouverte (API, webservices) afin de connecter facilement les innovations futures (IoT, IA, blockchain).
- Formez massivement les opérateurs : un taux d’adoption inférieur à 90 % réduit à néant les bénéfices escomptés.
Retour d’expérience : après déploiement d’un WMS SaaS multi-sites, un e-commerçant de mode a réduit son taux d’erreur d’expédition de 0,9 % à 0,11 % en trois mois, économisant 1,8 M€ de retours par an.
5. Appliquer les principes Lean et 5S sur les postes de travail
Le Lean Logistics vise à éliminer les mudas (gaspillages). Les résultats sont rapides :
- 5S (Seiri, Seiton, Seiso, Seiketsu, Shitsuke) pour avoir des postes propres et ordonnés.
- Kanban visuel afin de déclencher le réapprovisionnement des bacs à temps.
- Standard de picking limitant les mouvements inutiles (regroupement par batch, “pick & pack” en une seule fois).
- SMED logistique (Single-Minute Exchange of Die) : optimisation des changements de–code commande ou de station d’emballage.
Pour solidifier la démarche :
- Animez un Gemba Walk quotidien : manager et opérateurs visitent un poste, identifient un irritant et le résolvent sous 48 h.
- Mettez en place des Andon boards numériques : problème levé, temps de résolution, responsable. Vous créez un cercle vertueux.
Impact santé & sécurité : la révision des hauteurs de cueillette (zone “golden zone” entre 60 cm et 160 cm) diminue de 40 % les TMS (troubles musculo-squelettiques).
6. Automatiser intelligemment : convoyeurs, AGV et robotique collaborative
L’automatisation n’a de sens que si le ROI est clairement défini et mesuré. Exemples d’équipements courants :
- Convoyeurs modulaires pour transporter cartons et bacs sur de longues distances.
- AGV/AMR (robots mobiles autonomes) qui déplacent palettes ou étagères vers les opérateurs.
- Bras cobotiques pour la palettisation ou la préparation des commandes e-commerce.
- Shuttles ou mini-load pour la haute densité et la productivité sur les petits articles.
Étapes d’un projet d’automatisation réussi :
- Étude de flux et de variabilité : si votre taux de variation journalière > 35 %, optez pour des solutions flexibles (robots « goods-to-person »).
- Pilote limité (POC) sur un flux test. Vous validez l’ergonomie, l’IT, la maintenance.
- Modèle hybride : automatisez 80 % des volumes réguliers et traitez 20 % de cas hors-gabarit en manuel. La surcharge robotique coûte vite cher.
Indicateur clé : le coût de préparation par ligne (€/ligne) doit baisser après automatisation. Contrôlez avant/après.
7. Optimiser la préparation de commandes : de la méthode ABC au slotting dynamique
Le slotting consiste à attribuer la meilleure position de stockage à chaque SKU.
- Vitesse de rotation.
- Poids/volume.
- Compatibilité produits (ADR, denrées alimentaires, températures).
- Accord réglementation (pharma, duty free, produits sensibles).
Un slotting dynamique proposé par le WMS permet de réviser cette allocation de façon périodique et d’éviter l’engorgement des allées lors des pics saisonniers.
Pour aller plus loin :
- Segmentez la préparation (mono-commande, multi-commande, on-demand “one-hour delivery”).
- Couplez slotting et transport : l’ordre de picking doit refléter la tournée du livreur (méthode “reverse-TMS”).
- Mesurez la fatigue opérateur : un pas inutile coûte plus qu’une seconde machine, surtout en grand entrepôt.
Benchmark : un vendeur en ligne d’électronique a réduit de 28 % son temps de cycle en générant chaque nuit un nouvel algorithme de slotting à partir des prévisions de commandes J+1.
8. Piloter la performance grâce à des KPI précis et partageables
KPI | Objectif | Fréquence | Responsable |
---|---|---|---|
Taux de service | > 99 % | Hebdo | Responsable logistique |
Productivité picking | > 120 lignes/h | Quotidien | Chef d’équipe |
Taux d’erreur d’expédition | < 0,2 % | Mensuel | Qualité |
Rotation stock (jours) | < 35 j | Mensuel | Demand planner |
CO₂/logistique (kg expédié) | -10 %/an | Trimestriel | Responsable RSE |
La visualisation sous forme de tableau de bord (Power BI, Qlik, Google Data Studio) permet un suivi collaboratif et réactif :
- Tableaux big-screen dans l’entrepôt pour que chacun voie le score du jour.
- Alertes push sur smartphone quand un KPI franchit un seuil critique.
- Analyse causale semestrielle pour corréler l’évolution des indicateurs et ajuster les plans d’action.
9. Intégrer la dimension RSE dans l’optimisation flux entrepôt
Les attentes sociétales et réglementaires incitent à :
- Réduire les déplacements carbonés par un zoning optimal et l’usage de véhicules électriques intra-site.
- Minimiser les emballages (carton sur-mesure, calage papier, éco-conception).
- Valoriser les déchets (compacteurs, filière REP, recyclage plastique).
- Améliorer l’ergonomie (luminaires LED, réduction du bruit, postes ajustables en hauteur).
Les bénéfices vont au-delà de l’environnement :
- Diminution de la taxe sur les déchets ou TGAP.
- Fidélisation des collaborateurs (marque employeur).
- Nouveaux marchés : certains donneurs d’ordre exigent une notation RSE minimale.
Zoom finance : un green warehouse peut bénéficier d’aides régionales (certificats d’économie d’énergie, subventions ADEME) pour le remplacement d’équipements frigorifiques ou d’éclairages.
10. Former et impliquer les équipes : clé de la réussite durable
Un projet d’optimisation flux entrepôt ne s’inscrit pas uniquement dans la technologie ; il repose avant tout sur l’humain.
« Un entrepôt bien conçu ne vaut que s’il est convenablement utilisé. »
Actions recommandées :
- Plans de formation continue (sécurité, WMS, bonnes pratiques de manutention).
- Système de suggestions ou kaizen event pour impliquer chaque opérateur dans l’amélioration.
- Indicateurs de compétences pour adapter la polyvalence et la montée en charge.
- Programme “buddy” : chaque nouvel arrivant est coaché par un pair référent les premières semaines.
Statistique clé : les entrepôts pratiquant la polyvalence (+ 3 postes par opérateur) réduisent l’absentéisme de 25 % et améliorent la productivité de 18 % en période de pics.
Checklist finale avant déploiement
✔ Flux cartographiés et zone de stockage dimensionnée.
✔ WMS paramétré avec adressage et slotting dynamiques.
✔ Processus Lean et 5S déployés.
✔ Automatisation ciblée justifiée par un ROI (< 4 ans idéalement).
✔ KPI partagés quotidiennement.
✔ Plan RSE intégré (green warehouse).
✔ Equipes formées et engagées.
Conclusion
L’optimisation flux entrepôt est une démarche transversale mêlant analyse, organisation, technologie et management. Elle permet de réduire les coûts opérationnels, d’améliorer la disponibilité des stocks et de délivrer un service client irréprochable. Dans un marché toujours plus exigeant, ceux qui investissent aujourd’hui dans des entrepôts agiles et connectés se dotent d’un avantage durable et difficile à imiter.
Vous souhaitez aller plus loin ? Commencez par un audit terrain puis priorisez les actions à fort impact : rapidité de mise en œuvre, retour sur investissement et alignement sur la stratégie globale seront vos meilleurs guides pour bâtir une logistique d’excellence.
Enfin, n’oubliez pas que la performance d’un entrepôt est un voyage permanent : mesurez, apprenez, ajustez… et recommencez !