À l’heure où la chaîne d’approvisionnement se digitalise à grande vitesse, l’entrepôt automatisé s’impose comme le pivot de la logistique moderne. Capable de fonctionner 24 h/24 et 7 j/7 tout en réduisant les erreurs, il permet aux entreprises de faire face à la croissance du e-commerce, aux tensions sur le marché de l’emploi et aux exigences toujours plus élevées des consommateurs.
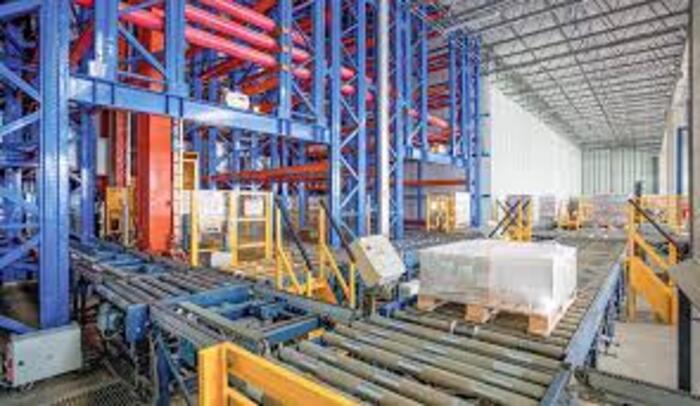
1. Qu’est-ce qu’un entrepôt automatisé ?
Un entrepôt automatisé est une installation dans laquelle la majorité – voire la totalité – des opérations (réception, stockage, préparation, emballage, expédition, inventaire) est réalisée par des systèmes mécatroniques et pilotée par un logiciel de gestion d’entrepôt (WMS). Les opérateurs ne se consacrent plus aux tâches répétitives ; ils surveillent, analysent, optimisent et interviennent seulement en cas d’aléa.
Le niveau d’automatisation peut être progressif : manuelle → semi-automatisée → automatisée → autonome. À chaque étape, des briques technologiques viennent s’ajouter pour fluidifier le flux et réduire les interventions humaines.
2. Les briques technologiques indispensables
2.1 Systèmes de stockage automatisé
- Transstockeurs palettisés : grues bicolonne ou monocolonne pour des hauteurs jusqu’à 45 m, charges ≤ 1 500 kg.
- Miniloads pour bacs ou cartons : vitesse de translation jusqu’à 6 m/s, jusqu’à 600 doubles cycles/heure.
- Shuttles multiniveaux : navettes ultrarapides dans des rayonnages denses, idéales pour la modularité.
- Silos autoportants : structure auto-stabilisée où le rayonnage fait office de bâti du bâtiment.
2.2 Transport interne sans caristes
Convoyeurs motorisés, véhicules à guidage automatique (AGV) et robots mobiles autonomes (AMR) assurent la circulation continue des unités de charge entre les quais, les zones de stockage et les postes de préparation.
- AGV filoguidés : fiables pour des trajets fixes, coût d’installation faible.
- AGV laser : navigation par LIDAR, flexibles, cartographie rapide.
- AMR à IA embarquée : détection d’obstacles en temps réel, re-planification dynamique.
- Convoyeurs curva pour les changements d’orientation sans perte de cadence.
2.3 Robotisation du picking, de l’emballage et de la palettisation
Bras articulés, cobots, trieurs haute cadence et cellules d’emballage intelligentes constituent l’épine dorsale de la robotisation de la préparation de commande.
- Bras delta : picking d’articles légers jusqu’à 120 cycles/minute.
- Ligne d’emballage adaptive : découpe et pliage de cartons sur mesure pour réduire les vides.
- Palettisation mixte : robot capable de constituer simultanément plusieurs palettes multi-références.
- Contrôle vision : caméras 2D/3D pour vérifier la conformité colis en temps réel.
2.4 Le cerveau numérique : WMS, WCS & MES
Le WMS (Warehouse Management System) orchestre les priorités logistiques tandis que le WCS (Warehouse Control System) traduit les ordres du WMS en mouvements physiques. Le MES (Manufacturing Execution System), lorsqu’il est présent, synchronise l’entrepôt avec la production.
Les logiciels modernes reposent sur des micro-services, des API REST et des tableaux de bord en cloud. L’intégration avec l’ERP assure une vision temps réel des stocks, des ordres clients et des niveaux de service.
2.5 IoT, capteurs et cybersécurité
Des capteurs de vibration, de température, de charge et de position remontent des millions de points de données. Ces données alimentent des algorithmes prédictifs qui déclenchent maintenance ou ré-ordonnancement. La connexion massive des équipements exige une cybersécurité “by design” : segmentation réseau, protocoles chiffrés, pare-feu industriels et mises à jour OTA (Over-The-Air).
3. Pourquoi automatiser son entrepôt ?
Les avantages d’un entrepôt automatisé se déclinent sur plusieurs axes :
- Productivité continue : fonctionnement sans interruption ni perte de cadence lors des pics de saisonnalité.
- Réduction drastique des erreurs : traçabilité numérique à chaque étape, taux d’erreur de préparation inférieur à 0,1 %.
- Optimisation de l’espace : rayonnages plus hauts et allées plus étroites, jusqu’à 40 % de surface gagnée.
- Sécurité renforcée : suppression des croisements entre engins et piétons, moins d’accidents.
- Durabilité : consommation énergétique réduite grâce aux moteurs à récupération d’énergie et à l’éclairage limité.
- Prévisibilité financière : coûts de main-d’œuvre stabilisés, amortissement long terme.
- Image de marque employeur : attractivité pour les profils techniques et rétention des talents.
« D’après le cabinet McKinsey, l’automatisation peut diminuer les coûts d’exploitation d’un entrepôt de 20 à 40 % tout en ramenant le lead time de traitement des commandes à quelques minutes. »
4. Étapes clés d’un projet d’entrepôt automatisé
4.1 Analyse des flux et de la demande
Un audit des historiques de ventes, des prévisions, des contraintes physiques (surface, hauteur libre, zone urbaine) et des profils de commandes détermine le dimensionnement optimal de l’installation. On y inclut :
- La cartographie des flux, temps de séjour, rotations ABC-XYZ.
- L’analyse de sensibilité aux pics et promotions.
- Le calcul de la capacité tampon et du taux de service cible.
4.2 Conception, simulation et jumeau numérique
Les fournisseurs et intégrateurs recourent à des jumeaux numériques pour tester différents scénarios de capacité, de performance et d’extension future. Les KPI simulés : saturation navettes, cadence WCS, temps d’attente quais, consommation d’énergie.
4.3 Sélection des prestataires et contractualisation
L’appel d’offres compare :
- Technologie (shuttle vs. miniload vs. cube-based storage).
- Garantie de disponibilité (SLA ≥ 99,5 %).
- Plan de maintenance et stock de pièces.
- Offres de robot-as-a-service ou de financement locatif.
4.4 Intégration du WMS et conduite du changement
Le choix du WMS est central : connecteurs API, gestion multi-sites, module de slotting, VMI, e-commerce, WES. La conduite du changement inclut formations, pilotage par la donnée et communication interne.
4.5 Phase de ramp-up et optimisation continue
La montée en cadence progressive limite les risques. Des indicateurs en temps réel (UPH, OEE, TRS) balisent l’optimisation continue. Une boucle PDCA (Plan-Do-Check-Act) devient la routine hebdomadaire.
5. Retours d’expérience – cinq cas inspirants
5.1 Industrie agro-alimentaire : la plate-forme froide « FrigoNord »
FrigoNord a remplacé son stockage semi-automatique par un entrepôt automatisé autoportant de 30 m de hauteur (-25 °C). Résultat : +60 % de capacité, traçabilité SDR (« Serial Data Record ») en temps réel et réduction de 35 % de la consommation d’énergie grâce à l’isolation renforcée et aux transstockeurs régénératifs.
5.2 Cosmétique & e-commerce : le hub omnicanal de « Beauté+ »
La marque gère 50 000 références avec un miniload, des AMR pour le picking et un module IA pour l’ordonnancement. Le taux de service est passé de 96 % à 99,8 %, crucial pour fidéliser des consommateurs exigeants.
5.3 Pièces détachées automobile : la plate-forme modulaire « AutoFlex »
AutoFlex a opté pour un shuttle system évolutif : 20 navettes aujourd’hui, 40 d’ici trois ans. Le projet, financé via un modèle OPEX (robot-as-a-service), a réduit la barrière d’entrée initiale.
5.4 Santé & dispositifs médicaux : « MediTrack »
Conformité GMP / GDP et sérialisation sont assurées par un WMS validé et des scanners 2D haute résolution. Les coffrets sensibles sont stockés dans des armoires AS/RS à atmosphère contrôlée (15–25 °C). Le taux de non-conformité a chuté de 87 %.
5.5 Vins & spiritueux : « Chai 4.0 »
Cet entrepôt automatisé bois-métal protège 12 millions de bouteilles. La robotique gère également la rotation barrique. Un algorithme IA anticipe la demande saisonnière et planifie les enlèvements douaniers.
6. Bonnes pratiques pour maximiser le ROI
- Modularité : prévoir des travées ou blocs supplémentaires pour accompagner la croissance sans arrêt de production.
- Maintenance prédictive : capteurs IoT et IA pour anticiper l’usure et éviter les pannes.
- Green logistics : récupération d’énergie au freinage des transstockeurs, panneaux photovoltaïques sur la toiture autoportante, relamping LED connecté.
- Formation continue : actualisation des compétences des techniciens et des superviseurs logiciel.
- Analyse de données : exploitation des logs WMS pour détecter goulets et opportunités d’optimisation.
- Plan de secours : procédures manuelles simplifiées et stock d’urgence pour garantir la continuité d’activité.
7. Combien coûte un entrepôt automatisé ?
Le coût varie fortement selon la capacité, la cadence, l’environnement (froid, explosif) et le degré d’autonomie recherché. Quelques repères :
- Mini-entrepôt shuttle 3 000 bacs : 800 000 € à 1,2 M€.
- Entrepôt autoportant 10 000 palettes : 5 à 8 M€.
- Plate-forme robotisée 60 000 bacs (e-commerce) : 15 à 20 M€.
- Projet clé en main avec robot-as-a-service : abonnement mensuel 0,15 € à 0,25 € par mouvement.
L’analyse de rentabilité doit inclure les gains cachés (réduction des ruptures, baisse des litiges, valorisation du foncier, diminution de la pénibilité) et appliquer un horizon pluriannuel (7-10 ans).
8. Futur de l’entrepôt automatisé : IA, 5G, cobotique évolutive et réalité augmentée
Les entrepôts de demain seront hyper-connectés. La 5G supplantera le Wi-Fi pour des échanges bas-latence entre robots, tandis que l’IA optimisera la micro-planification en temps réel. Les opérateurs utiliseront des lunettes de réalité augmentée pour configurer les machines ou résoudre des alarmes sans appeler la maintenance.
On voit émerger la cobotique évolutive : des modules robotiques ré-affectables d’une zone à l’autre selon la saison. Les drones d’inventaire réaliseront les comptages de nuit, et le blockchain garantira l’intégrité des mouvements de stock sensibles.
9. Réglementation et certifications
Automatiser ne dispense pas de respecter les normes : EN 528 pour transstockeurs, EN 15635 pour rayonnages, ISO 27001 pour la sécurité des systèmes d’information, SEVESO pour les entrepôts chimiques. Les assurances exigent souvent des certifications FM Global concernant la résistance au feu et les sprinklers ESFR.
10. Conclusion : vers une logistique plus résiliente et durable
L’entrepôt automatisé n’est plus réservé aux géants de l’industrie. Grâce à la baisse du coût des capteurs, à la flexibilité des shuttles et aux offres cloud du WMS, les PME investissent à leur tour dans cette technologie pour gagner en compétitivité. En automatisant intelligemment, vous transformez votre entrepôt en un centre névralgique résilient, agile et durable.
Vous envisagez de passer à l’automatisation ? Visitez le portail Logistique 360 pour accéder à des livres blancs, des simulateurs de ROI et échanger avec notre communauté d’experts.